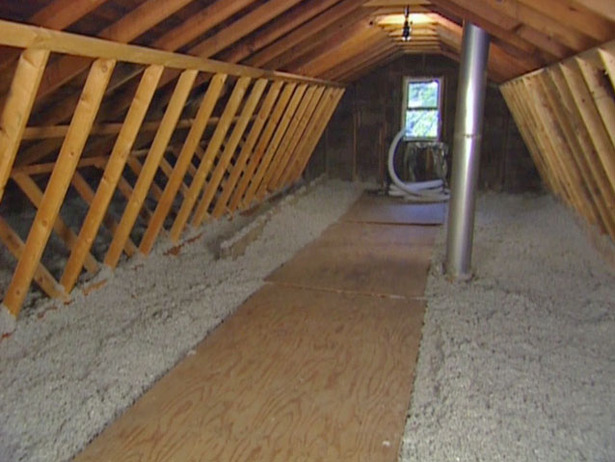
Cellulose Insulation has gained its reputation worldwide as the most environmentally friendly insulation and is fast becoming a popular choice for insulating homes.
Cellulose Insulation has gained its reputation worldwide as the most environmentally friendly insulation and is fast becoming a popular choice for insulating homes.
For every 1% not covered = 5% loss in insulation effectiveness. With its’ loose fill properties – cellulose insulation can provide 100% coverage by insuring no gaps in the installation.
Blown In Cellulose Insulation Is:
• Fire & Pest Resistant
• Manufactured from recycled paper
• Great acoustic properties
In a demonstration experiment testing the difference between Cellulose Insulation and Fiberglass Insulation, Cellulose Insulation reduced an alarm of 125 decibels to 40 decibels. The fiberglass insulation did reduce the noise level as well, but only to 75 decibels.
Cellulose insulation materials fulfill these requirements perfectly. A higher degree of sound-wave absorption correlates to a higher longitudinal flow resistance. The sound wave travelling through the insulation material experiences friction when coming into contact with the fibres which results in a higher resistance level. The sound energy (in the form of air pressure) is thereby transformed into heat energy. The sound energy that is transformed can no longer be heard on the other side.
Blown in cellulose insulation easily flows around obstructions and penetrates odd shaped cavities and it easily conforms around wires, electrical boxes and pipes.
Blown in cellulose insulation is 2-3 times denser than fiberglass insulation.
We specialize in low pitch, Rake, flat and skillion ceilings that are inaccessible to most other insulation types
MUCH HIGHER SOUND DENSITY RATING
Many residential structures contain large amounts of wood. Cellulose insulation is the only wood-based building material that is always treated with fire retardant and is vermin Proof.
Insul-Guard only uses cellulose that has been treated with non-toxic Borax and Boric acid that is manufactured in our own factory to Australian standards this makes cellulose insulation one of the safest materials used in home construction.
If a fire occurs, the dense structure of cellulose and its fire retardants slow its spread through the building by blocking flames and hot gases and restricting the availability of oxygen in insulated ceilings. Air and fire roar right through fiberglass. This is due to the most flammable tar used on the paper vapor barrier and the low density of fiberglass batts which doesn’t block air movement. Several fire demonstrations have been conducted in which cellulose-insulated structures have remained virtually intact while uninsulated and mineral-fiber insulated structures burned to the ground.
We offer our services to all residential and commercial
1. Cellulose is the oldest building insulation material. Many types of cellulosic materials have been used, including newspaper, cardboard, cotton, straw, sawdust, hemp and corncob. Monticello was insulated with a form of cellulose. Modern cellulose insulation, made with recycled newspaper using grinding and dust removing machines and adding a fire retardant, began in the 1950s and came into general use in the US during the 1970s.
2. The market for insulation increased following the oil embargo of 1973-74. The embargo caused energy costs for heating to skyrocket across the nation, which led to increased interest in energy conservation measures. Insulation gained significant national attention as a cheap and available technology to increase the energy efficiency of homes. In 1977, following a particularly severe winter, a tax credit was given for homeowners who installed insulation.
3. While in 1976 there were roughly 100 cellulose insulation firms with 125 plants, by 1978 there were more than 350 firms with more than 500 plants1. Cellulose insulation was produced locally by small manufacturers who purchased ready-to-operate machines and offered a cheap and easy low-tech production process. Other than some constraints created by a shortage of boric acid for use as fire retardant, cellulose captured an increased share of the market due to lower costs and its suitability for retrofits. Meanwhile fiberglass and rockwool producers found it difficult to keep up with the demand for insulation from their customers.
Currently cellulose insulation has increased again in use in the United States. Part of the reason for this growth are studies that suggest that cellulose may actually protect a building from damage in a fire better than fiberglass because cellulose is denser than fiberglass and doesn’t allow the oxygen necessary to burn structural members. Several National Research Council Canada studies [2] have backed these claims. Another major reason for the comeback of cellulose might be because of the increased interest in green building. Cellulose has the highest recycled content of any insulation material and also has less embodied energy than fiberglass and other furnace produced mineral insulations.
The thermal performance of loose filled cellulose compares favorably to other types of insulation. The thermal conductivity of loose-fill cellulose is approximately 40 mW/m•K (an R-value of 3.8 per inch) which is about the same as or slightly better than glass wool or rock wool. This doesn’t represent the whole picture of thermal performance. Other important aspects are how well the building envelope is sealed from air infiltration, convective airflows, and thermal bridging.Cellulose is very good at fitting around items in walls like pipes and wiring, leaving few air pockets that can reduce the overall efficiency of the wall
SOUND INSULATION
Noise reduction is achieved in three ways with cellulose. The first is that cellulose completely fills cavities leaving few air pockets for sound to travel in. The second is the cellulose material’s ability to trap air. The significant difference between noise reduction with cellulose and fiberglass is its density. Cellulose is approximately three times denser then fiberglass. This helps deaden the sound through walls and between floor levels.
FIRE RETARDATION
The borate treatment also gives cellulose the highest (Class I) fire safety rating.
RECYCLED CONTENT
Cellulose is composed of 75-85% recycled paper fiber, usually post-consumer waste newsprint. The other 15% is a fire retardant such as boric acid or ammonium sulphate. Cellulose has the highest recycled content of any insulation available. For example, fiberglass has a maximum amount of 30% recycled content.
The non-recycled components of cellulose insulation are still environmentally preferable to the raw materials of most other insulation types. Unlike foam insulations, many of which use HFC or HCFC blowing agents which have global warming potential hundred or thousands of times higher than that of carbon dioxide, cellulose does not produce significant gaseous emissions.
Cellulose has great advantages for industrial health and worker safety. Toxicity of the raw materials of most insulation types is typically highest during manufacture or installation. Neither is an issue with cellulose.
The sole hazard of cellulose according to the categorization by the OSHA is that it is a dust nuisance, requiring a simple dust mask during installation. This compares very favorably to the potential NIOSH cancer risk of fiberglass Embodied energy
CALCULATE SAVINGS FROM INSULATION
You can now measure the financial impact of increasing your insulation performance by entering your data into our easy-to-use insulation calculator. By entering in the size of your house, the current and desired R-value you want from your insulation and the cost of your energy, you can see immediately what you would be saving this year and for years to come.
As an added feature, you can also see how your insulation decisions can impact your CO2 emissions.
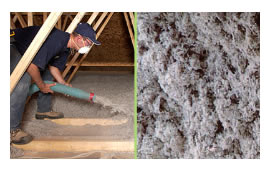